Questo articolo affronta i diversi aspetti da considerare per garantire il corretto funzionamento delle pompe.
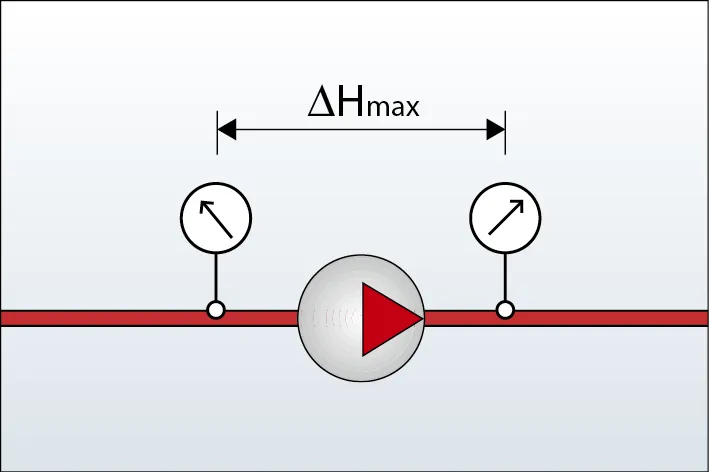
Non è facile determinare la giusta prevalenza massima in base a cui vanno regolate le pompe, in quanto generalmente sussistono sensibili differenze fra la teoria e quanto in pratica realizzato.
La difficoltà crescono ulteriormente nei casi di riqualificazione, specie se non si conosce, o si conosce solo in parte, la geometria dell’impianto.
Fino a pochi anni fa, queste indeterminazioni (per essere sicuri di poter far fronte alle perdite di carico dell’impianto) portavano a regolare le pompe con prevalenze superiori del 30÷40% rispetto a quelle effettivamente necessarie.
Di conseguenza le pompe così regolate funziona-vano, e funzionano tuttora, con costi di gestione, molto più elevati di quelli richiesti.
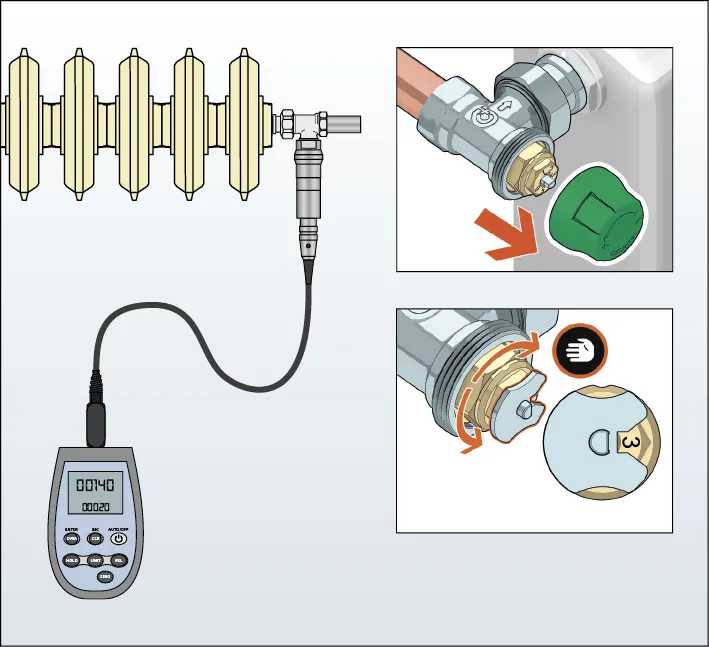
Da alcuni anni è però possibile (consultare Idraulica 51 e Idraulica 52) evitare tali sprechi utilizzando valvole di tipo DYNAMICAL® CON KIT di supporto in grado di consentire la misura dei loro ΔP di lavoro.
Col kit è possibile dapprima misurare il ΔP di lavoro della valvola più sfavorita (in genere la più lontana) e poi regolare la prevalenza della pompa in modo da far lavorare la valvola col ΔP minimo richiesto.
Con simile regolazione sussiste la certezza che tutte le altre valvole dell’impianto lavorano con il ΔP minimo richiesto e che pertanto sono in grado di minimizzare sia i costi di gestione delle pompe sia l’insorgere di pressioni in rete troppo elevate.
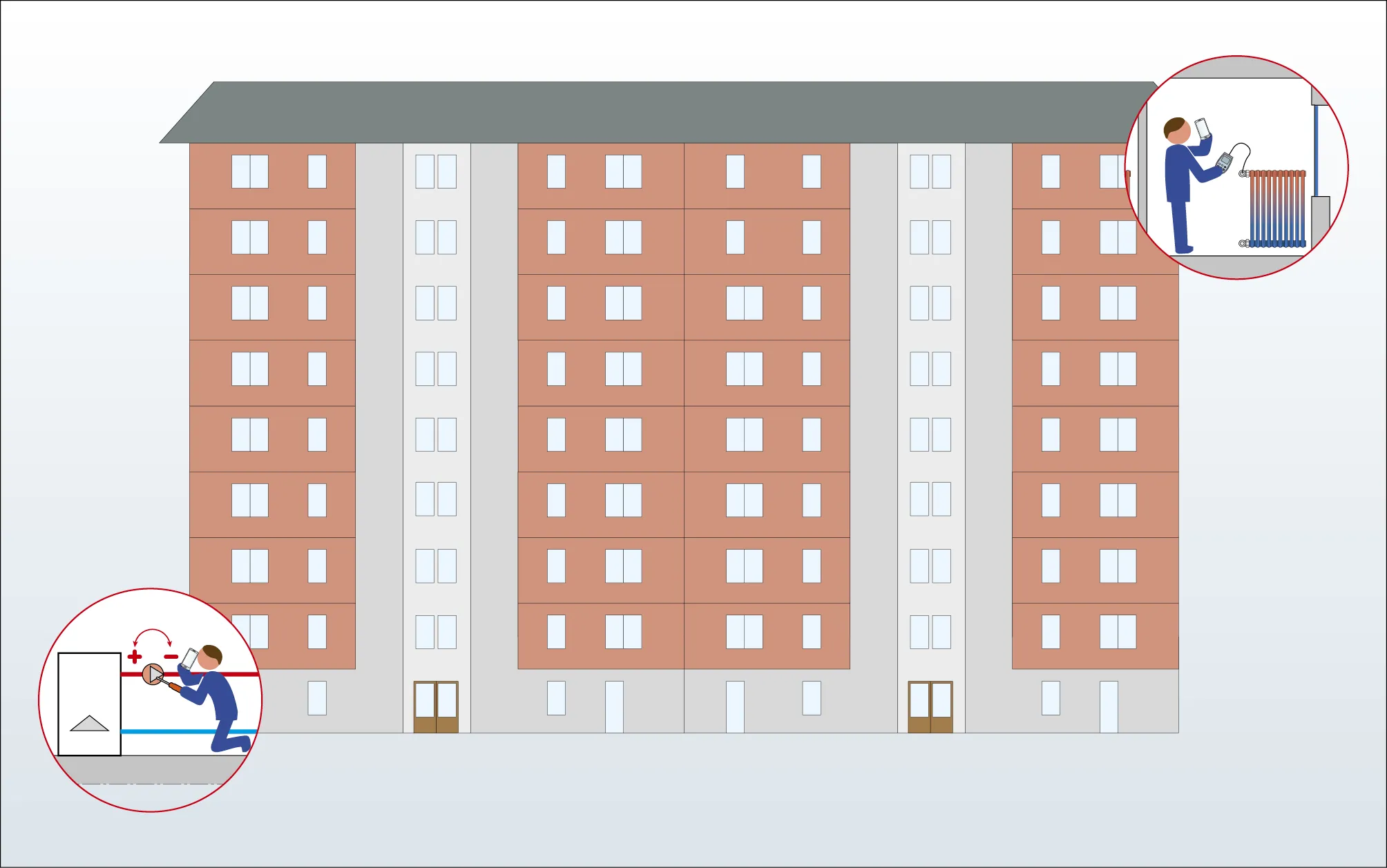
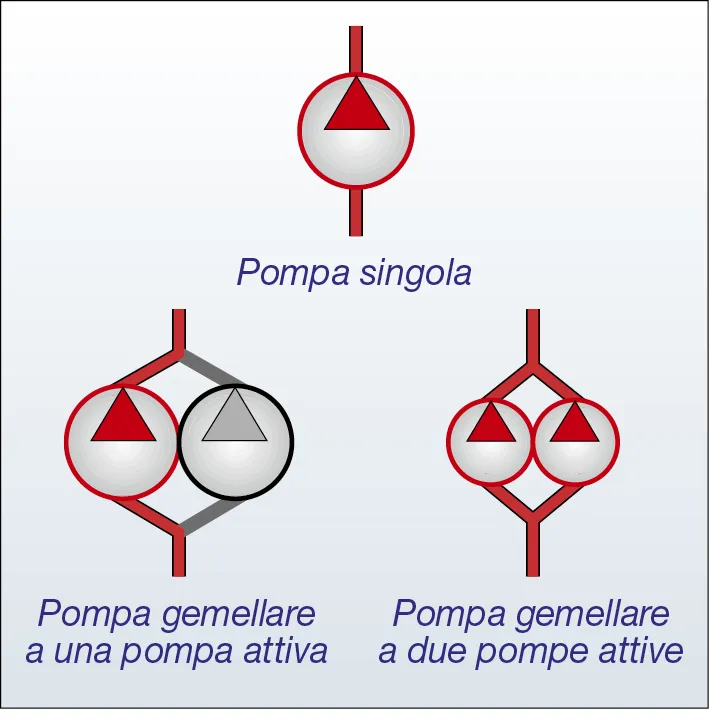
Il dimensionamento delle pompe va effettuato in base alle portate e alle prevalenze di calcolo. Le pompe devono essere scelte evitando sia, per ovvi motivi, i sottodimensionamenti sia i sovradimensionamenti in quanto fanno lavorare le pompa in zone a bassa efficienza.
In base alle esigenze o meno di continuità del servizio, possono essere utilizzate pompe singole o gemellari:
Le singole (le meno costose) possono essere utilizzate in impianti che non temono in modo parti-colare possibili interruzioni del riscaldamento.
Le gemellari a una pompa attiva (le più costose) consentono, anche in caso di rottura di una pompa, il regolare funzionamento dell'impianto;
Le gemellari a due pompe attive possono essere un buon compromesso tra i costi e le prestazioni di cui sopra, perché, anche in caso di rottura di una pompa evitano il blocco totale dell'impianto.

I circolatori devono essere installati su tubi orizzontali o verticali con l'albero motore disposto in posizione orizzontale.
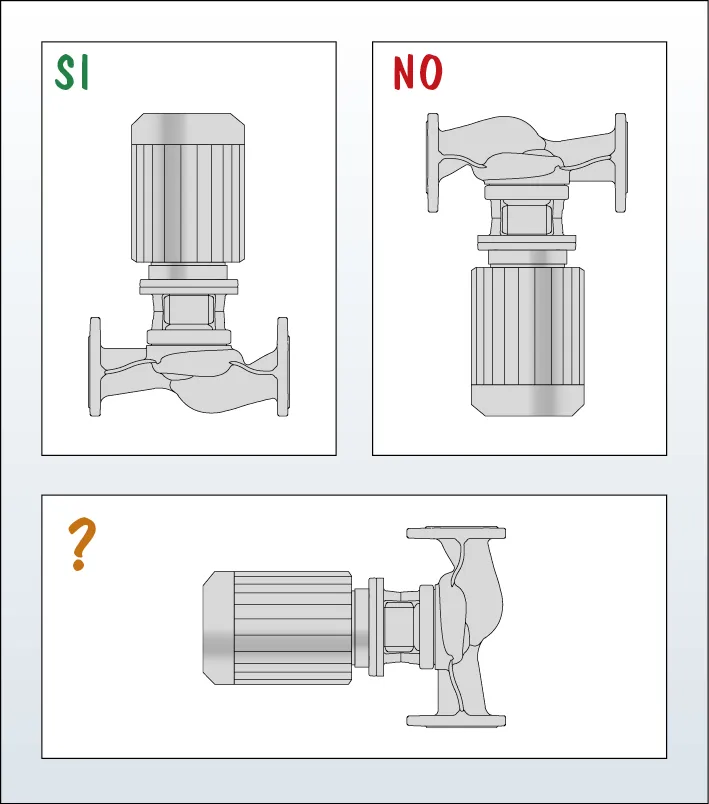
Le pompe con potenze inferiori a 10÷12 kW (ved. comunque le prescrizioni dei Costruttori) possono essere installate su tubi sia orizzontali sia verticali.
Le pompe, invece, con potenze superiori possono essere installate solo su tubi orizzontali e con motore verticale.
I motori non devono essere rivolti verso il basso.

Come sappiamo le pompe sono esposte ai pericoli della cavitazione. Questo fenomeno si manifesta quando, nella zona di aspirazione della pompa, la pressione del fluido scende al di sotto del suo punto di pressione satura, cioè del suo punto di ebollizione. Al verificarsi di tale condizione, si formano in continuo bolle e microbolle d’aria che collassano, implodendo nel liquido.
Il tutto avviene in modo molto rapido e provoca gravi anomalie di funzionamento della pompa con forti rumori, vibrazioni e danni alla girante e al corpo pompa. Negli impianti di riscaldamento la cavitazione si verifica soprattutto quando la pompa richiede una prevalenza elevata e l’impianto ha basso carico statico.

Per evitare tale pericolo è necessario garantire un valore minimo di pressione all’ingresso della pompa: valore individuato da un apposito in-dice: l’NPSH (Net Positive Suction Head) che dipende dal tipo di pompa e dalle condizioni di funzionamento, e soprattutto dalla temperatura del fluido e dalla pressione atmosferica.
In merito generalmente i Produttori danno il valore dell’indice NPSH in relazione alle portate della pompa. Va comunque verificato se tali valori sono riferiti alle condizioni di funzionamento dell’impianto oppure se si deve tener conto di appositi parametri correttivi in merito.

Sono necessari quando è richiesta una portata minima per garantire il corretto funzionamento della pompa.
A tal fine è consigliabile by-passare direttamente la pompa e regolare la portata del by-pass con un AUTOFLOW® avente portata nominale uguale a quella minima richiesta.
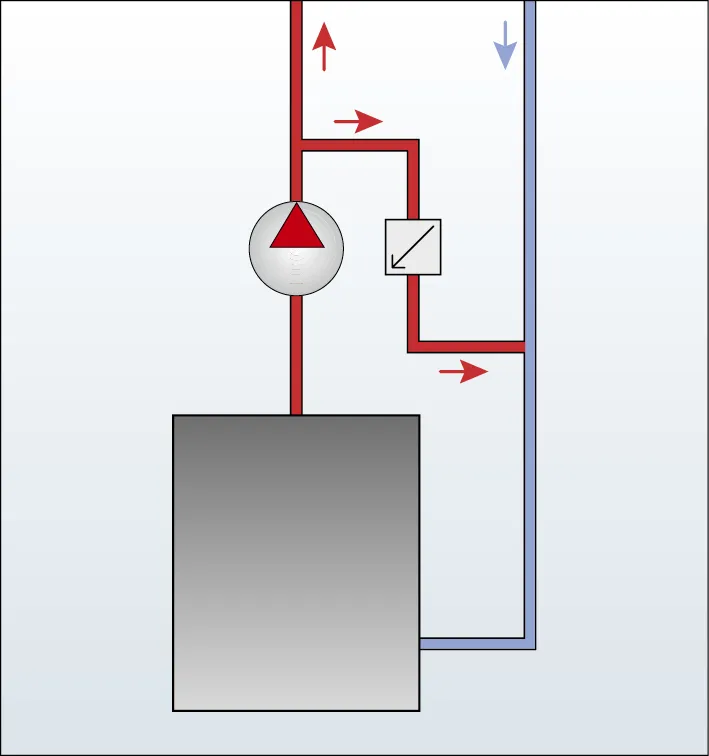
Non è consigliabile, invece, realizzare by-pass con un collegamento diretto fra l'andata e il ritorno dell'impianto, in quanto comporterebbero un innalzamento della temperatura di ritorno e, quindi, una minor resa delle caldaie a condensazione.
Per quanto riguarda le pompe, l’aria presente negli impianti può provocare due problemi:
- il primo è dovuto alla possibilità che si formino sacche d’aria sul lato di aspirazione delle pompe, con conseguente minor resa e maggior usura delle pompe stesse;
- il secondo è invece dovuto al fatto che l’ossigeno, presente nell’aria, si lega a qualsiasi materiale di ferro, formando ossidi che possono comportare, oltre alla minor resa, anche il blocco e “la bruciatura” delle pompe.
Come già considerato in merito (consultare Idraulica 37 e Idraulica 45) tali problemi possono essere risolti eliminando non solo le bolle ma anche le microbolle d’aria. A tal fine possono essere utilizzati appositi disaeratori: componenti costituiti essenzialmente da una rete disposta a raggiera e da una valvola di sfogo aria.
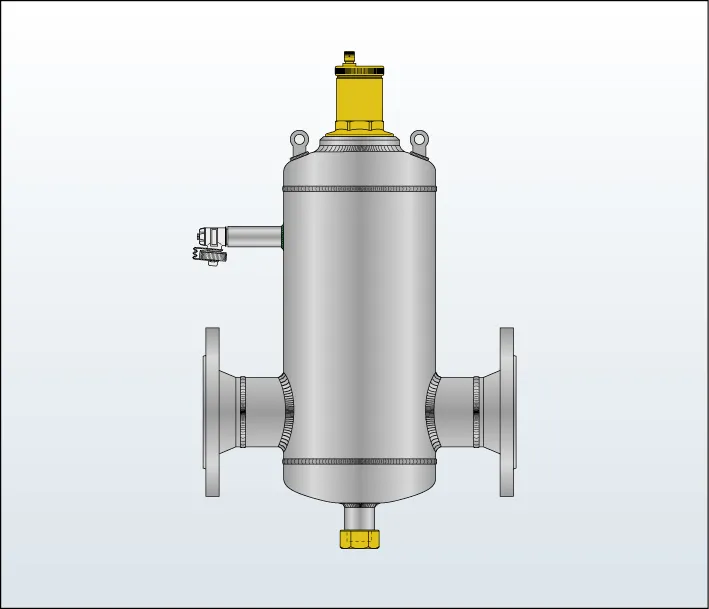
La rete crea moti vorticosi che favoriscono la liberazione delle microbolle e la loro fusione in bolle eliminabili dalla valvola di sfogo aria.
I disaeratori fanno funzionare gli impianti con acqua impoverita d’aria e pertanto in grado di assorbire, e poi eliminare, le bolle d’aria annidate nelle zone critiche degli impianti.
Le pompe sono prodotti di precisione con elementi in costante movimento. Ed è, per queste loro caratteristiche, che possono essere facilmente messe in crisi dalle impurità, incrostazioni e prodotti di corrosione normalmente presenti nell'acqua dell'impianto.
Tali sostanze comportano, infatti, un notevole incremento degli attriti interni e quindi possono causare sia il blocco, sia la "bruciatura", delle pompe stesse: pericoli che sono ancora più temibili con i nuovi circolatori perché hanno dimensioni più ridotte e funzionano con velocità più elevate.
Pertanto, oltre a pulire accuratamente l’impianto prima del suo avvio e a “caricarlo” con acqua idoneamente trattata, bisogna cercare di limitare il più possibile i fenomeni di corrosione dell’impianto. Qui di seguito presenteremo i principali.

Si verifica in varie forme che vanno dagli attacchi uniformi su ampie zone di superficie a gravi attacchi locali. È il tipo di corrosione che cede al fluido la maggior quantità di metallo ossidato.

La corrosione di una superficie metallica può essere accelerata dall’erosione (cioè dall’asportazione puramente meccanica del metallo) causata dal flusso del fluido. Le zone più esposte a questo pericolo sono quelle ad elevata velocità e forte turbolenza.

È una forma particolare di corrosione causata, come abbiamo già visto, dall’implosione di bolle in prossimità delle superfici metalliche: implosione che produce onde di pressione in grado di provocare forti erosioni localizzate.
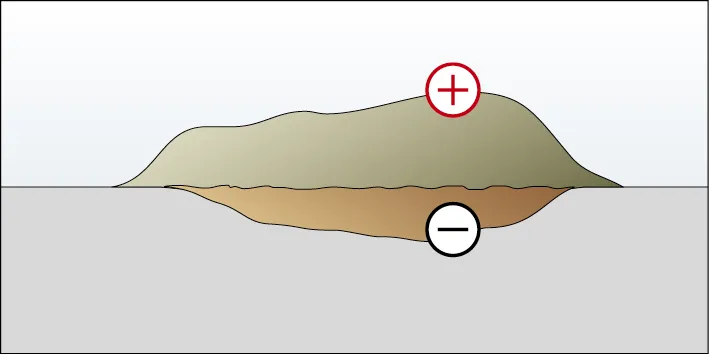
Questa corrosione (detta anche corrosione sotto depositi) si verifica in zone dove le velocità di scorrimento del fluido sono molto basse e, quindi, dove possono formarsi depositi di sporco.
L’azione corrosiva è dovuta al fatto che, in presenza di acqua, un deposito di sporco, su una superficie metallica, forma due strati (acqua/sporco e sporco/metallo) con diverso tenore di ossigeno: situazione questa che attiva, fra i due strati, pile localizzate in grado di corrodere la superficie metallica.
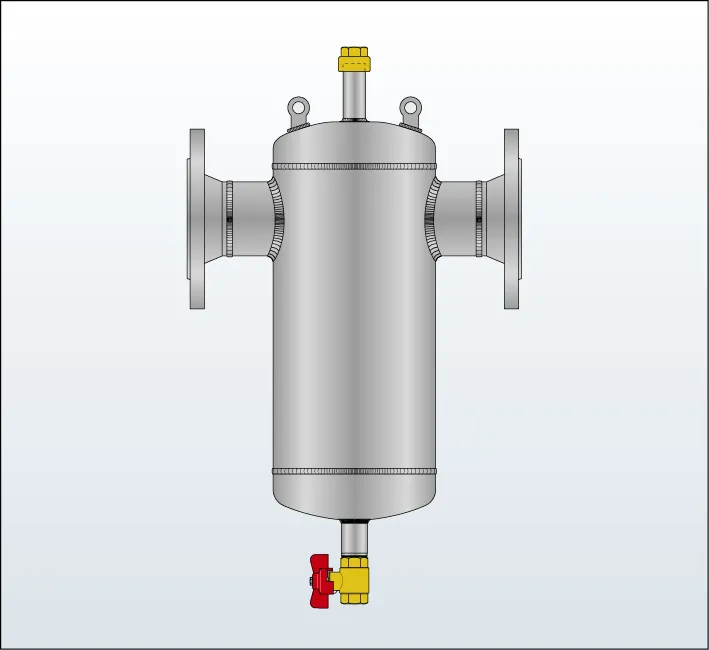
Va considerato che, negli impianti di riscaldamento, è praticamente inevitabile che si formino residui solidi di corrosione. Pertanto è bene prevedere l’uso di defangatori magnetici (consultare Idraulica 45).